大同SMC不飽和聚酯塑料生產
發布時間:2023-04-21 01:38:49
大同SMC不飽和聚酯塑料生產
DMC模塑料、BMC模塑料、SMC模塑料是以不飽和聚酯為基體,加入增強纖維、無機粉體填充、苯乙烯交聯劑、熱塑性樹脂低收縮率添加劑、脫模劑、引發劑等組成的增強復合材料;和傳統的玻璃鋼(FRP)不同之處在于:玻璃鋼是樹脂+增強纖維兩種組分,而模塑料是樹脂+增強纖維+填料三種組分。模塑料按制品結構和加工方法的不同,可分為BMC模塑料、DMC模塑料、SMC片狀模塑料,其性能相差不大。

大同SMC不飽和聚酯塑料生產
塑料材料模塑過程中膨脹和收縮量的大小與所加工塑料的熱膨脹系數有關,模塑過程的熱膨脹系數稱為“模塑收縮”。隨著模塑件冷卻收縮,模塑件與模腔冷卻表面失去緊密接觸,這時冷卻效率下降,模塑件繼續 冷卻后,模塑件不斷收縮,收縮量取決于各種因素的綜合作用。模塑件上的尖角冷卻快,比其它部件更早硬化,接近模塑件中心處的厚的部分離型腔冷卻面遠,成為模塑件上較慢釋放熱量的部分,邊角處的材料固化后,隨著接近制件中心處的熔體冷卻,模塑件仍會繼續收縮,尖角之間的平面只能得到單側冷卻,其強度沒有尖角處材料的強度高。制件中心處塑料材料的冷卻收縮,將部分冷卻的與冷卻程度較大的尖角間相對較弱的表面向內拉。這樣,在注塑件表面上產生了凹痕。

大同SMC不飽和聚酯塑料生產
模壓時間也稱壓縮模塑保溫保壓時間。是指模具完全閉合到模具開啟之間,物料在模內受熱固化的時間。模壓時間在成型過程中的作用主要是使獲得模腔形狀的成型物有足夠的時間完成固化。固化是指熱固性塑料成型時體型結構的形成過程,從化學反應的本質來看固化過程就是交聯反應進行的過程。但工藝上的“固化完全”并不意味著交聯反應已進行到底,即所有可參加交聯的活性基團已全部參加反應。這一術語在工藝上是指交聯反應已進行到合適的程度,制品的綜合物理力學性能或其他特別指定的性能已達到預期的指標。顯然,制品的交聯度不可能達到100%,而固化程度卻可以超過100%,通常將交聯超過完全固化所要求程度的現象稱為“過熟”,反之稱為“欠熟”。

大同SMC不飽和聚酯塑料生產
模壓時間的確定與SMC/BMC模塑料的固化速率,制品的形狀和壁厚、模具的結構、模壓溫度和模壓壓力的高低,以及預壓、預熱和成型時是否排氣等多方面的因素有關,在所有這些因素中以模壓溫度、制品壁厚和預熱條件對模壓時間的影響更為顯著。合適的預熱條件由于可加快物料在模腔內的升溫過程和填滿模腔的過程,因而有利于縮短模壓時間,提高模壓溫度時模壓時間隨之縮短而增大制品壁的厚度則要相應延長模壓時間。在模壓溫度和模壓壓力一定時模壓時間就成為決定制品性能的關鍵因素,模壓時間過短樹脂無法固化完全、制品欠熟因而力學性能差,外觀缺乏光澤,脫模后易出現翹曲和變形等。適當延長模壓時間不僅可克服以上的缺點,還可使制品的成型收縮率減小并使其耐熱性、強度性能和電絕緣性能等均有所提高。但過分地延長模壓時間又會使制品過熟,不僅生產效率降低、能耗增大而且會因過度交聯使收縮率增加,導致樹脂與填料間產生較大的內應力;也常常使制品表面發暗起泡,嚴重時會出現制品破裂。

大同SMC不飽和聚酯塑料生產
隨著科技的發展,片狀模塑料(SMC)在汽車工業中的應用量不斷提升,同時對SMC模塑料的要求也逐漸提高,主要從原材料配方和成型工藝兩個方面探討了如何降低SMC模塑料的收縮率、改善制品的表面質量,來制備具有低收縮率(<0.05%)、A級表面質量及優良力學性能的高性能SMC復合材料。通過原材料的科學匹配,選擇z佳配方,SMC片材生產工藝的嚴格控制(如樹脂糊中水分和粘度的控制),優化SMC模壓工藝參數(如選擇合理的鋪料方式、兩段式壓制、合理的加壓時機等),壓制出高品質的SMC汽車制品。
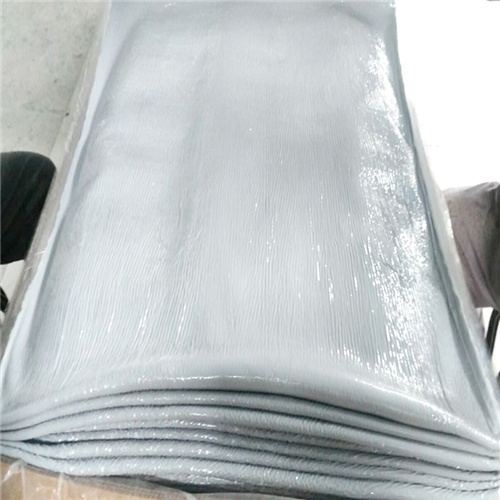
大同SMC不飽和聚酯塑料生產
樹脂:適合于制備SMC的樹脂有不飽和聚脂(占主導地位)、乙烯基脂樹脂、環氧樹脂、酚醛樹脂等。1、不飽和聚脂樹脂:適合于SMC的不飽和聚脂的品種很多,可按照制品的使用要求選擇樹脂:(1)要求制品具有A級精度的間苯型聚脂SMC;(2)韌性SMC:對于要求耐沖擊強度高的制品,如汽車部件、保險杠、轉動軸、彈簧等,需要用韌性SMC;(3) 低密度、高強度的SMC:對于要求輕質高強的制品,如汽車頂篷等,需要密度小而強度高的SMC來制作。在這種SMC的配方中,特別是含有空心玻璃微珠,此微珠的密度為0.46g/cm,直徑為10~100цm,其加入量約為樹脂質量的20%;(4) 低收縮率的SMC:有關低收縮率SMC的配方中必須加入低收縮劑;(5) 通用型SMC;(6) 結構型SMC;(7) 高強度型SMC(HMC):這種高強度型SMC的組成特點是樹脂的浸漬性好,玻纖的質量特別高,大約是樹脂質量的2倍左右。